









Introduction to BGA Test Seat
Source:
Author:
Introduction to BGA Test Seat
BGA is an IC package that increases the capacity by two to three times without changing the memory capacity, and is usually used for memory chips. Compared with TSOP chips, BAG chips are smaller in size and have better heat dissipation and electrical performance. The frequency of use has also greatly increased, a lot of BGA chip in the patch, do not know whether it is stuck or the chip itself is bad, there will be the motherboard does not boot, and maintenance, usually need to replace BGA, to analyze the reason. In order to verify whether the IC is OK, we need to use tools to test, so the tools for testing BGA are what we call BGA test fixture, BGA test seat, BGA test rack, etc.
And the BGA package chips on the market can be said to be very different from the package PIN number, size, spacing and other aspects. Hony's existing BGA test seat in addition to commonly used points, some not commonly used most need to be customized. Foreign BGA test seat customization generally needs 4-6 weeks, and our company only needs 1 week. Compared with foreign test seat, more cost-effective, better. Probe mechanical test life is not equal to the actual service life of the probe, because the mechanical test is the use of probe test, and in the laboratory dust-free environment, the use of mechanical vertical pressure, so long life; And the actual test use, often hundreds of roots, thousands of roots used at the same time, due to the precision of machining, can not guarantee that each probe parallel to each other, absolute vertical; In addition, the pressure of each manual test can not be maintained evenly, so during the test process, the probe pressure may not be the same, resulting in some probe pressure is too large, will be damaged, thus affecting the test life; In addition, the test environment is often dust, tin slag debris accumulated for a long time, will plug the needle seam, so the test seat and test fixture service life is different, according to the specific use, there is no unified standard, but can replace the probe to extend the service life; Some BGA test seat may have an internal short circuit, in the process of testing, resulting in too much current, resulting in probe burn probe, needle tray and other accessories burn out, even burn out the customer's PCBA board, so before the power test to ensure that the BGA test seat without internal short circuit; A kind of gray solid material, radiation resistance, insulation stability, hydrolysis resistance, compression resistance, corrosion resistance, the mechanical parts made of the composite material has the effect of self-lubrication, when reinforced with 20% ~ 30% glass fiber, thermal deformation temperature can be increased to 280 ~ 300℃ high temperature resistance, good thermal stability, high heat resistance (better than PPS).
Drilling plate and floating plate are the core parts of socket, which play the role of fixing probe and guiding chip. They often wear out during testing, so the material requirements are very high. At present, the commonly used materials on the market are FR4, Torlon PAI, PEI, PPS, PEEK + ceramics, etc. Long time test, easy to appear the phenomenon of test instability, has been slowly eliminated, compared with the other four engineering materials, good wear resistance, and has self-lubrication.
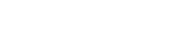
Lanyi Electronics - Semiconductor Test Probe Manufacturing Plant
Customer first, quality first, unity and cooperation, mutual benefit and win-win






Copyright © 2022 Dongguan Lanyi Electronic Technology Co., Ltd. All Rights Reserved. 粤ICP备17061266号 Powered by www.300.cn SEO