









BGA test seat production process
Source:
Author:
BGA test seat production process
After using BGA test seat for a long time, some tin slag or dust will remain on the tip of the needle, resulting in unstable test; You can use an anti-static brush, dipped in anhydrous alcohol, gently brush the residue on the probe, if conditions can be used to blow the socket probe area, the effect is better; All custom test seats and test fixtures, if in normal use, are provided with three months of free maintenance, because the probe is worn parts, according to the actual use; The probe burns out or other parts are damaged due to the high current caused by the short circuit inside the chip, which is not covered by the free warranty; For products with a free warranty period of more than three months, paid maintenance services will be provided according to the actual situation. Custom BGA test seat process. Understand the packaging parameters and test requirements of the corresponding chip of the customized BGA test seat; The sales staff will sort out the customer information and send it to the engineering evaluation department for feasibility evaluation and quotation. After the customer confirms the structure, scheme and quotation and pays the deposit, the business department will arrange the order, and the relevant engineer department will send the product information of customized BGA test seat to the design department, and ask the design department to make DWG/PDF drawings and BOM list. Then feed back to the chief engineer for confirmation. The engineer will ask the customer to confirm the drawing. When they confirm that this BGA test seat product meets their needs, they will move on to the next product. When the customer confirmed that the drawing was correct, they also began to arrange the BGA test board according to the drawing. The design department will ask CNC programmers to make CNC programs, and the materials department will prepare raw materials. (The production of customized tooling/mold shell shall be arranged by the chief engineer). Injection molding Department: After mold and material inspection, these materials are sent to the injection molding department for the production of plastic body and related parts (such as materials, plastic particles, springs or POGO inspection by IQC). Check the mold. After confirmation, the mold engineer will check the mold quality and check the mold quality during the inspection. When they find mold problems, they use mirror spark machines to fix them. Numerical control department: After the numerical control program is normal, it is sent to the numerical control machine for testing, and then waits for the mold or traditional plastic parts to enter the drilling hole and other graphic numerical control production (numerical control inspection is completed by the two-dimensional graphic machine).
After all the results are correct, the parts go into the assembly room for installation (the assembler examines the BGA test seat through a microscope). Perform QC system inspection according to FEMA shown. The custom production process of BGA test seat fixture (that is, according to the customer's current product PCBA board, the IC socket is directly fixed on the product accurately, without layout, greatly reducing the testing cost, widely applicable to ODM/ semiconductor FEA department IC verification), we will introduce separately later. Please follow us regularly. We will provide more information on BGA test seat, burn-in seat and test fixture.
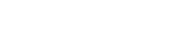
Lanyi Electronics - Semiconductor Test Probe Manufacturing Plant
Customer first, quality first, unity and cooperation, mutual benefit and win-win






Copyright © 2022 Dongguan Lanyi Electronic Technology Co., Ltd. All Rights Reserved. 粤ICP备17061266号 Powered by www.300.cn SEO